One of the most relevant clothing manufacturers in Romania, Tanex differentiates itself in the market by providing comprehensive customer support. The company has made the leap from simply fulfilling customer orders to producing finished products, a process that includes prototyping, sample making, negotiation and procurement of raw materials, production, logistics and delivery. In this way, the company has succeeded in increasing its added value in relation to globally renowned customers in France, Spain and the UK. In 2020, Tanex exceeded €12 million turnover, with two centres with 7,500 sqm of production area, around 400 employees and over 750,000 products delivered monthly.
In 2019, clothing manufacturer Tanex decided to invest in a modern ERP and opted for Microsoft Dynamics NAV. With ELIAN, the company upgraded its entire data management and reporting system so that management has visibility and control over the business.
The benefit of information-driven decisions was seen in 2020, when the company achieved a 15% increase in profitability.
Business challenges
Established in 1999, Tanex has grown steadily in terms of both production means and capacity and business processes. However, the IT system has not kept pace with this development. The company used four separate applications (accounting, production, payroll, document management) purchased at different stages and lacking integration. As a result, users were entering data redundantly into all these applications and management did not have an overview of the business. Two pressing problems arose from this: the high workload of clerical staff and the impossibility of quickly correlating stock with production and supply, which is critical when dealing with products comprising between 50 and 100 items.
The IT system was outdated, we were entering data into four separate applications, but we had no activity visibility. Getting a report was difficult and it took up to a month to put together all the information needed to support a decision. Furthermore, at an operational level, we were unable to match existing stocks with production requirements and supply orders, which affected workflow and led to missed deadlines. Clearly, we needed better organisation.
Antonio Bajenaru, Chief Financial Officer, Tanex
TANEX chooses ELIAN
After an initial attempt at integrating existing applications, Tanex management realised they needed a powerful ERP system to help grow the business.
The first step was to research the main suppliers, supplemented with recommendations solicited from business partners who owned factories or industrial production facilities. The company short-listed the vendors and solutions it was looking for, and finally chose to work with ELIAN and Microsoft Dynamics NAV.
ELIAN’s experience in manufacturing environments and understanding of processes specific to the apparel industry, as well as the level of functionality and customization of Dynamics NAV, were key factors in the decision.
Between the suppliers evaluated we chose ELIAN because the team had real experience in companies operating factories and production workshops. The references presented convinced us that they had the capacity to carry out such a project. The proposal of a Microsoft solution also mattered, because after working with several local applications, we realised that a global manufacturer has a different perspective on technology and is a long-term guarantee.
Antonio Bajenaru, Chief Financial Officer, Tanex
After the decision…
After the decision to purchase was made, Tanex requested a fast rhythm of implementation so that the system would be ready at the beginning of the new fiscal year. The process included an extensive business analysis with discussions by department (Purchasing, Sales, Finance – Accounting, Production) and workshops to identify the most accurate requirements and develop particular workflows where needed. Some modules were implemented at standard level, but others were heavily customised or built from scratch. The most complex developments were made in the modules for production planning and capacity booking, employee activity normalisation and material consumption optimisation. Integration with JetReports, to increase the accuracy of managerial reports, and with a payroll application for time recording data, was also carried out. At the end of the project all users went through multiple training sessions, data was migrated to Dynamics NAV, and the old system was shut down.
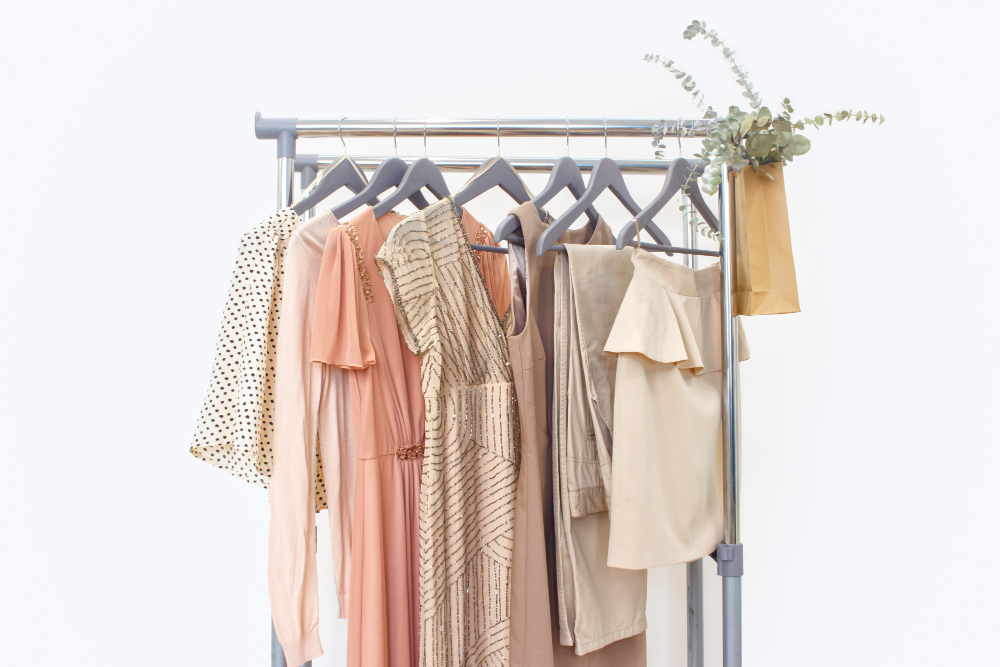
NAV helps increase profitability by 15%
After implementation, Tanex gained full visibility and control over the business. Dynamics NAV has become the dashboard where the management team finds the information needed to support strategic or operational decisions. In fact, in 2020, based on the data provided by Dynamics NAV, the company closely monitored cost and profit centers and made all necessary adjustments for operational optimization, which led to a 15% increase in profitability.
What Tanex gains by using Dynamics NAV
Benefits
Together with ELIAN, we have carried out a project with a great impact on Tanex’s activity. Implementing a modern ERP system may seem costly, but if we weigh the investment versus the benefits, we immediately understand that it is a justified and necessary step to increase economic performance and long-term development of any company.
Antonio Bajenaru, Chief Financial Officer, Tanex
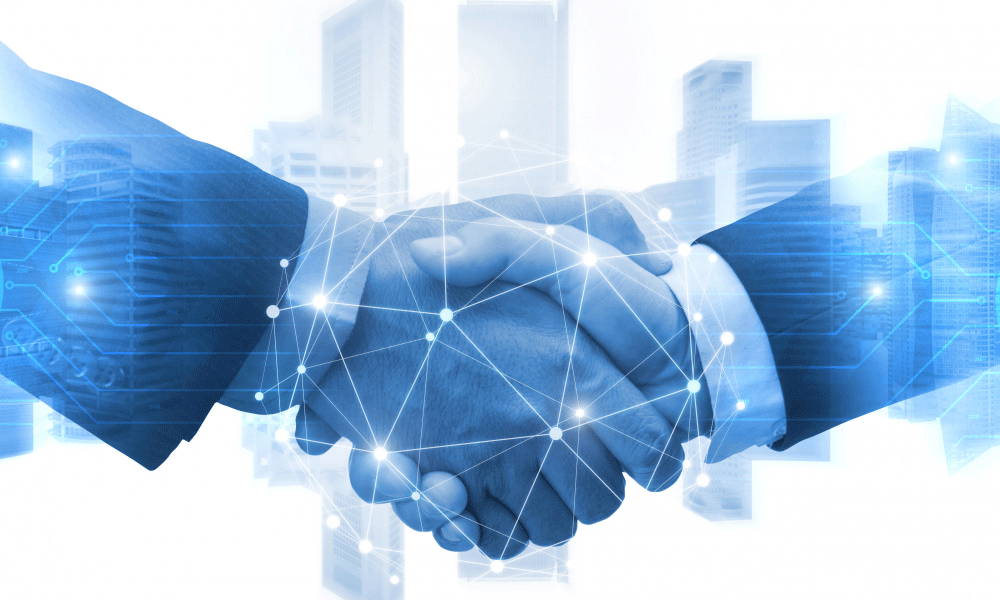