The Production module offers a complete solution for defining, monitoring and controlling production processes. It works in close correlation with the other modules (supply and sales), ensuring an integrated approach to the production process.
In order to convert a material into a finished product, production resources such as material invoices, routes, machine operators and the machine itself must be configured in the system.
When demand is planned and materials have been issued according to the production BOMs, the actual production operations can start and be executed in the sequence defined by the production order circuit.
From a system point of view, an important part of production execution is to record the outgoing production in the database to report progress and to update the inventory with finished items. Output can be recorded manually by filling in and recording log lines after production operations. It can also be done automatically with the backward flushing utility. In this case, material consumption is automatically recorded together with output when the production order changes to finished.
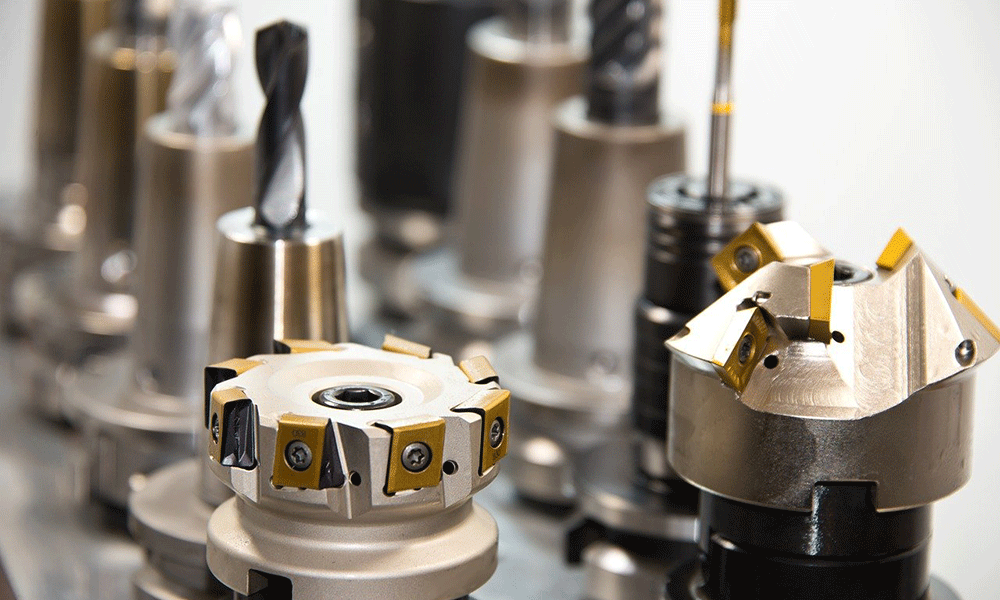
Among the features of the module we list:
* It works in close correlation with the other modules (supply and sales) ensuring an integrated approach to the production process.
* Allows the definition and management of production recipes and their versions, technological files and production capacities.
* Allows the creation and management of production orders for different production states:
a. Simulated – for the R&D department
b. Planned or firmly planned – for efficient planning of material requirements and production capacities
c. Launched – for operating stock changes resulting from the production process
d. Finalised – for history and further analysis
* Allows production orders to be created automatically, based on planning, directly from sales orders or manually.
* Allows serialisation or batching of both raw materials consumed and finished products produced.
* Allows the analysis of a production year based on components, production times and estimated set-up times per production batch.
* The cost of the finished product will be determined automatically on the basis of the actual consumption of raw materials and the cost of production time; indirect production costs can also be defined with fixed or percentage values.
* Certain indirect costs can be redistributed after the production process, according to user-defined distribution keys.
* Offers the possibility to plan production by stock, order or combined production
Cost: Reduce operational costs by automating the creation of production orders and the cost of finished product. Indirect costs can be redistributed later in the production process.
Time: Significantly reduces labour time through an integrated approach to the production process, creation and management of production orders, definition and management of production recipes.
Risk: Reduces business risk by enabling production forecasting, history and subsequent analysis, component-based production analysis of a production antecalculus
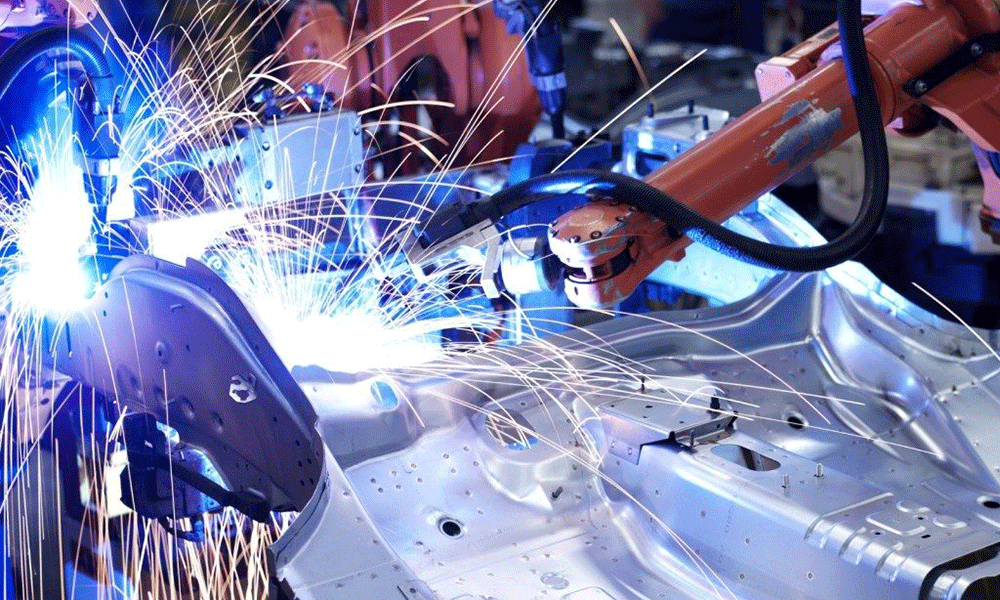